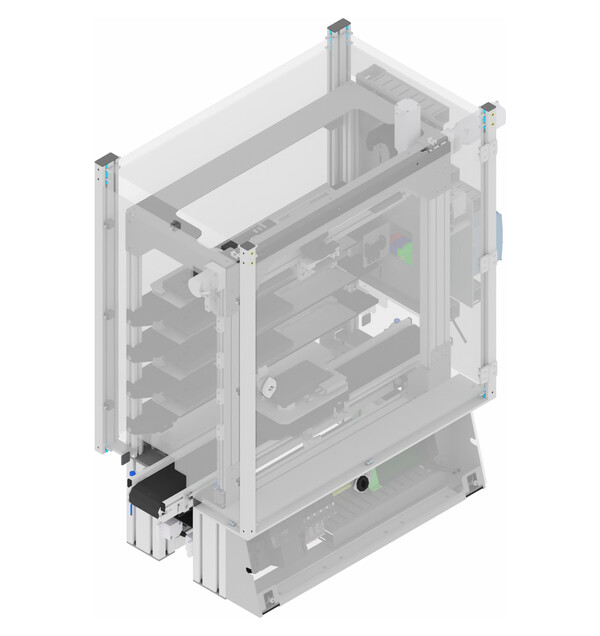
- General
-
Order number D13023 Type code CP-L-iASRS12-W-C12 Series CP Systems Categories Application module
- Description
-
The automatic warehouse for workpieces offers four levels with three storage bays each for housing workpieces. The storage and retrieval unit consists of a Cartesian kinematic system with two electric positioning drives, a pneumatic linear drive and a gripper.
The automatic warehouse for workpieces is designed as an intelligent subsystem with its own controller. Positioning is done by means of rapid/creep positioning and a rotary encoder. An additional locking device prevents the gripper from colliding with the shelves.
Only compatible with CP Lab base modules.
-
Attribute Value Dimensions (L x W x H) 766 mm x 376 mm x 610 mm Weight 18.3 kg Operating voltage 24 V DC Control modules Siemens SIMATIC CPU 1214C
SM 1223 8 DI/8 DOInterfaces PROFINET® -
Application module interface (Syslink or analog terminal)
Description Reference Datatype Address
CP LabAddress
CP FactoryInputs Auto (periodic square wave): Error / Teach: Teach mode active Bool %I0.0 %I2.0 Auto: Homing done / Teach: Position saved Bool %I0.1 %I2.1 Auto: Storing done / Teach: Y-axis extended into storage bay Bool %I0.2 %I2.2 Auto: Retrieval done / Teach: Gripper opened Bool %I0.3 %I2.3 Auto: Number of work pieces (Bit 0) / Teach: Next teaching position = Belt Bool %I0.4 %I2.4 Auto: Number of work pieces (Bit 1) / Teach: Next teaching position = Bay #1 Bool %I0.5 %I2.5 Auto: Number of work pieces (Bit 2) / Teach: Next teaching position = Bay #12 Bool %I0.6 %I2.6 Auto: Number of work pieces (Bit 3) / Teach: Teaching complete Bool %I0.7 %I2.7 Outputs Operating mode (0=automatic, 1=teach mode) Bool %Q0.0 %Q2.0 Auto: Start homing / Teach: Save position Bool %Q0.1 %Q2.1 Auto: Start storing / Teach: Extend y-axis into storage bay Bool %Q0.2 %Q2.2 Auto: Start retrieval / Teach: Open gripper Bool %Q0.3 %Q2.3 Auto: Storage bay bit 0 / Teach: Move right Bool %Q0.4 %Q2.4 Auto: Storage bay bit 1 / Teach: Move left Bool %Q0.5 %Q2.5 Auto: Storage bay bit 2 / Teach: Move up Bool %Q0.6 %Q2.6 Auto: Storage bay bit 3 / Teach: Move down Bool %Q0.7 %Q2.7 Integrated PLC
Description Reference Datatype Address Inputs X-axis encoder - channel A +CL-BG4:A Bool %I0.0 X-axis in reference position +CL-BG3 Bool %I0.1 Gripper closed +CL-BG11 Bool %I0.2 Z-axis encoder - channel A +CL-BG8:A Bool %I0.3 Z-axis in reference position +CL-BG7 Bool %I0.4 Y-axis retracted +CL-BG9 Bool %I0.5 Y-axis extended into storage bay +CL-BG10 Bool %I0.6 Storage bay empty +CL-BG13 Bool %I0.7 X-axis encoder - channel B +CL-BG4:B Bool %I1.0 Workpiece present on pallet +CL-BG14 Bool %I1.1 Z-axis encoder - channel B +CL-BG8:B Bool %I1.2 X and Z-axis disabled through sensor bar +CL-BG12 Bool %I1.3 Pallet present +CL-BG15 Bool %I1.4 Emergency stop OK 24NA Bool %I1.5 Outputs Move X-axis right +CL-QA1:A1 Bool %Q0.0 Move x-axis left +CL-QA1:A2 Bool %Q0.1 Enable x-axis creep speed +CL-QA1:A3 Bool %Q0.2 Move z-axis down +CL-QA2:A1 Bool %Q0.3 Move z-axis up +CL-QA2:A2 Bool %Q0.4 Enable z-axis creep speed +CL-QA2:A3 Bool %Q0.5 Extend y-axis into storage bay +CL-MB1 Bool %Q0.6 Open gripper +CL-MB2 Bool %Q0.7 -
-
-
-